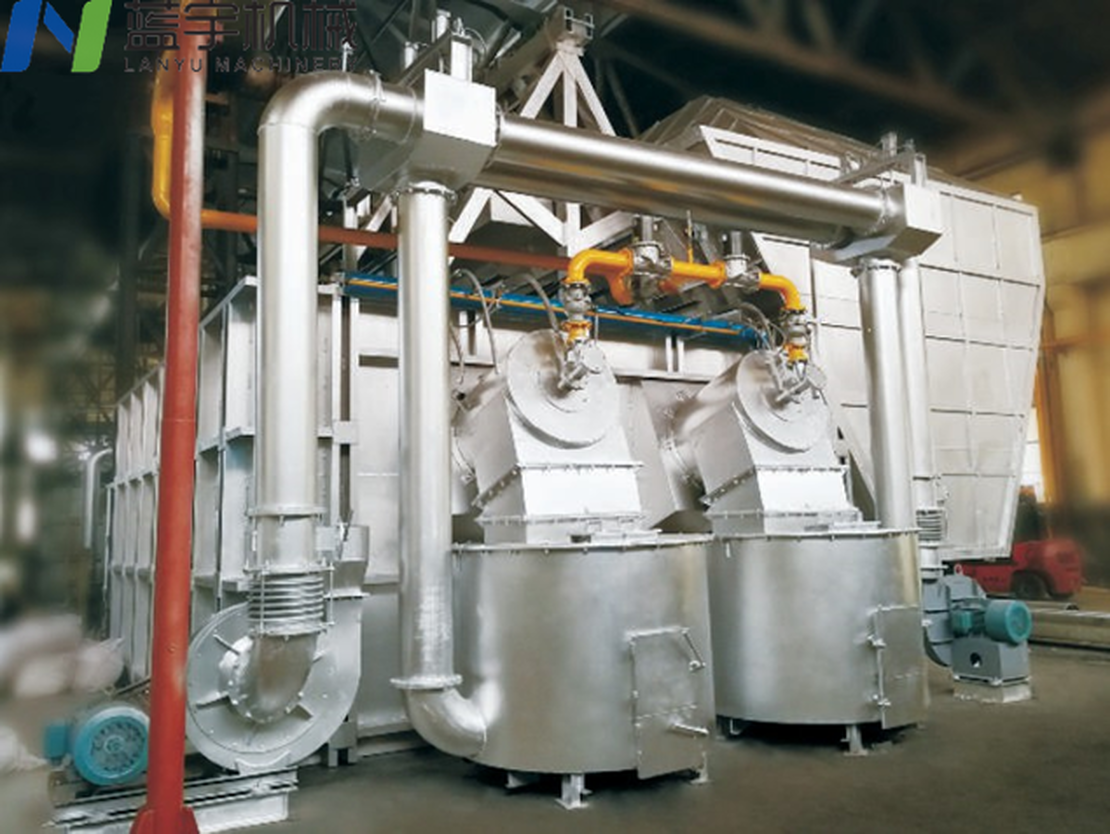
Energy Eficient Regenerative Combustion System
- Combustion system
- April 26, 2025
Table of Contents
Application Scope >
The Energy Eficient Regenerative Combustion System has extensive applicability and can be used with various non-ferrous metal melting furnaces,保温 furnaces, and heating furnaces. This system is primarily used for the pre-melting process of aluminum alloy ingots, zinc alloy ingots, aluminum alloy rods, aluminum plates/bands, aluminum wheels, and zinc-aluminum die-cast products. It is currently the most efficient, energy-saving, and environmentally friendly ideal choice.
Working Principle >
The Energy Eficient Regenerative Combustion System mainly consists of two burners (or 3, 4, 5, etc., multiple burners). Below is a detailed explanation of its working principle:
Workflow
Air Heating Phase
- Ambient temperature air from the auxiliary fan is switched into Regenerative Chamber A via a diverter valve.
- The air is rapidly heated by alumina balls in Regenerative Chamber A, with temperatures quickly rising to 600-800°C.
High-Temperature Air Injection
- The heated high-temperature air is then injected at high speed into the furnace through the burner, creating strong flames.
- High-temperature air mixes thoroughly with fuel, ensuring efficient combustion and intensity.
Exhaust Gas Handling Phase
- Hot exhaust gases from the furnace exit through Regenerative Chamber B.
- The high-temperature exhaust gases release heat in Regenerative Chamber B, heating the alumina balls to approximately 800°C.
Low-Temperature Exhaust Emission
- After heat exchange, the low-temperature exhaust gases (below 150°C) are expelled through the diverter valve, minimizing thermal loss to the environment.
Heat Switching and Alternating Operation
- When the regenerative media in one chamber reach their heat storage capacity, the diverter valve switches.
- The two regenerative combustion chambers alternate between heat absorption and release, maintaining a continuous cycle for energy efficiency and reduced consumption.
Key Components
- Burner: Responsible for injecting high-temperature air-fuel mixtures to generate strong flames.
- Diverter Valve: Controls the direction of airflow and exhaust gas flow, ensuring effective heat recovery and utilization.
- Regenerative Chamber A: Used for storing and releasing heat to warm incoming ambient air.
- Regenerative Chamber B: Handles high-temperature exhaust gases from the furnace while releasing stored heat to maintain system temperature.
- Alumina Balls: Core thermal storage medium with excellent heat resistance and stability.
Energy-Saving Benefits
- Significantly improves combustion efficiency through effective heat recovery.
- Reduces fuel consumption and lowers operational costs.
- Exhaust gas temperatures are below 150°C, meeting environmental standards while achieving energy-saving and emission-reduction goals.
This working principle not only enhances the efficiency of the combustion system but also achieves energy conservation and environmental protection effects, making it one of the most advanced combustion technologies available today.
Technical Features >
Switching Cycle: 30-120 seconds
The system ensures efficient operation and heat recovery with its rapid switching capability.Exhaust Gas Temperature at Discharge: Typically between 100-150°C, with a maximum of no more than 180°C
Low exhaust gas temperature complies with environmental regulations and reduces thermal energy waste.Energy Consumption per Ton of Aluminum Products: Can reach within 50 cubic meters, saving over 50% compared to traditional combustion methods
Significant reduction in energy consumption enables efficient and economical production.Flame Characteristics: Strong flames and stable combustion between intense and stable Combines high combustion intensity with stable operation for optimal performance.
Main Specifications >
100MK, 200MK, 300MK, 400MK, 500MK, 600MK