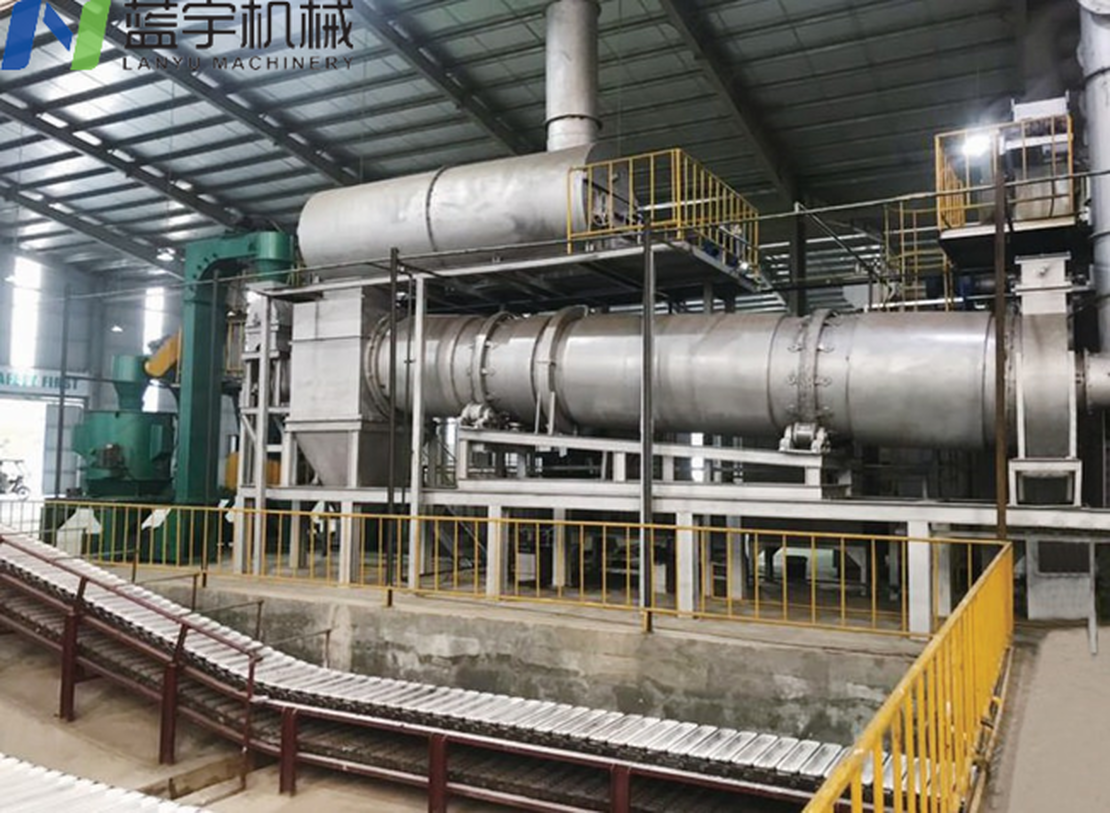
High Efficiency Preheating Kiln for scrap Aluminum
- Preheating kiln
- April 26, 2025
Table of Contents
Overview
The High Efficiency Preheating Kiln for scrap Aluminum is a new type of equipment developed based on the drum dryer. It is primarily designed to address the treatment of oil and moisture in waste aluminum, aluminum shavings before smelting, and to achieve effective preheating of materials. The equipment dries materials containing certain metallic substances (such as silicon carbide powder, iron shavings, raw iron shavings, iron powder, aluminum shavings, cans, raw and sintered aluminum, copper powder, steel shavings, ores, etc.) to a dry state before smelting, thereby achieving the goal of refining pure aluminum while effectively reducing energy consumption. This equipment is particularly suitable for drying large-particle, high-density materials in industries such as metallurgy, mining, and chemicals. The heat source can be flexibly selected based on requirements, using various fuels or utilizing industrial furnace flue gas to provide efficient thermal solutions tailored to different application scenarios.
Equipment Principle
Material Handling and Conveyance
Material Input
Materials containing oil and moisture are loaded into the storage hopper by forklift.Elevating Conveyance
The bucket elevator steadily conveys materials from the storage hopper into the preheating drum, ensuring smooth material flow.
Preheating and Drying Process
Preheating Drum Structure
Disturbance board are uniformly distributed inside the preheating drum to ensure even distribution and dispersion of materials within the drum.Heat Transfer
Materials in the drum come into full contact with hot air flowing in parallel or counter-current, accelerating heat transfer for efficient drying.Motion Control
Under the influence of inclined disturbance board and thermal airflow, materials are controllably moved to the other end of the preheating drum for finished product discharge.
Impurity Treatment
Centrifugal Dewatering and Magnetic Separation
Materials with high levels of oil, moisture, and impurities can undergo preliminary treatment using industrial centrifuges and magnetic separators before entering the storage hopper to further remove contaminants.Flexible Configuration
Depending on actual needs, centrifuges and magnetic separators can be added or omitted to ensure materials are in an ideal state upon entering the preheating drum.
Heat Source Description
- Heat Source Selection
Multiple fuels (such as natural gas, diesel, biomass, etc.) or industrial furnace flue gas can be selected as heat sources to provide flexible and efficient drying solutions.
Through these steps, materials containing oil and moisture are efficiently dried and preheated in the kiln, providing ideal raw materials for subsequent smelting processes.
Technical Features
Main Structure
- Component Composition: Storage hopper, bucket elevator, preheating drum, heat source (burner or industrial furnace flue gas), discharge machine, and control panel, etc.
- Material Selection: Suitable materials are applied to all components. The main structural steel is made of high-quality steel.
- Anti-deformation Design: The preheating drum is made of 16Mn boiler steel, effectively preventing deformation under high temperature conditions.
- Continuous Operation Capability: The equipment can operate continuously with a large production capacity.
Vortex Rolling Material Technology
- Unique Design: Adopting a vortex rolling material method to reduce resistance when hot air passes through the cylinder and increase the contact surface with materials
- Efficient Preheating: Provides faster preheating, lower energy consumption, and improved drying efficiency.
Diversified Heat Source
- Fuel Selection: In addition to using various fuels (such as natural gas, diesel, biomass, etc.) as heat sources, industrial furnace flue gas can also be utilized.
- Energy Efficiency: Flexible heat source selection enhances energy utilization and reduces costs.
Professional Design and Manufacturing
- High-Quality Components: All components are selected based on industry standards to ensure long-term stable operation.
- Customization Options: The equipment is modularly designed, allowing adjustments to capacity and configuration according to specific production needs.